Industrial Laundry Services vs. In-House Care for Workwear
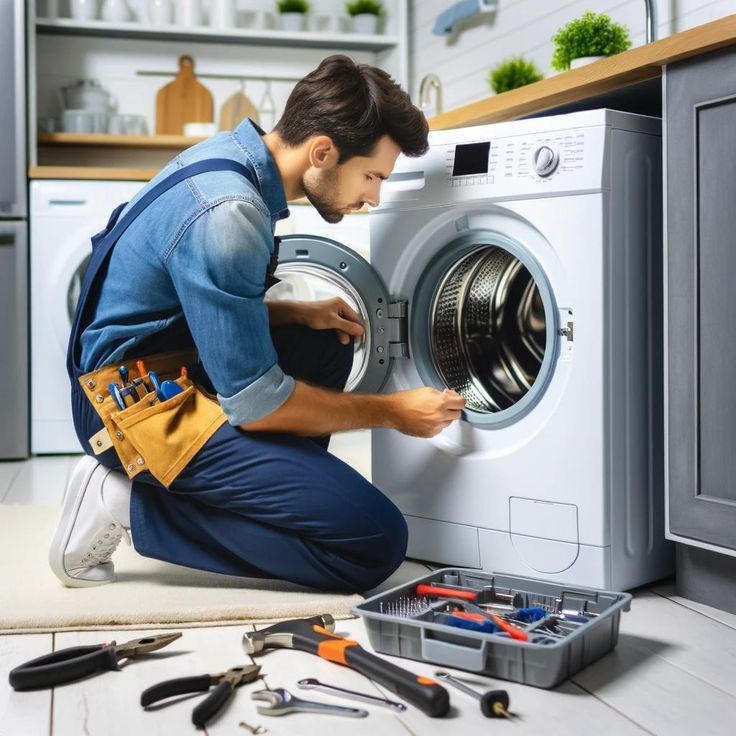
For industries across Saudi Arabia, the decision between outsourcing workwear maintenance to specialized industrial laundry services versus establishing in-house care facilities represents a significant operational and financial consideration. This choice impacts not only bottom-line costs but also workplace safety compliance, environmental footprint, and ultimately, workforce productivity and well-being.
The Evolving Landscape of Industrial Workwear Maintenance
The Saudi industrial sector has experienced dramatic growth across multiple sectors, driving increased demand for sophisticated workwear maintenance solutions:
- Market Expansion: The industrial laundry service market in Saudi Arabia has grown at a compound annual rate of 8.7% since 2018, reflecting increasing recognition of specialized maintenance requirements for technical workwear.
- Regulatory Evolution: Progressive implementation of stricter occupational safety standards under Saudi Vision 2030 initiatives has elevated requirements for workwear cleanliness, decontamination, and integrity verification.
- Technology Integration: Both commercial laundry operations and in-house facilities have seen substantial technological advancement, with automation, specialized chemical processes, and tracking systems transforming maintenance capabilities.
- Sustainability Focus: Growing environmental concerns have driven innovation in water reclamation, energy efficiency, and chemical management across both service models, though implementation varies significantly.
- Workforce Expectations: Increasing worker awareness of occupational health considerations has raised expectations for properly maintained workwear that delivers both comfort and protection.
Industrial Laundry Services: Advantages
Professional industrial laundry services offer several distinct benefits for Saudi organizations:
- Specialized Processing Capabilities: Access to industrial-grade equipment specifically designed for removing stubborn industrial contaminants, including oil-based compounds, chemical residues, and fine particulates that consumer-grade equipment cannot effectively address.
- Validated Decontamination Protocols: Implementation of scientifically validated cleaning processes that not only remove visible soiling but address microbial contamination and chemical residues that could present occupational health hazards.
- Scale Efficiency: Economic advantages through processing volumes that enable significant reductions in per-garment costs for utilities, chemicals, and labor compared to smaller in-house operations.
- Regulatory Compliance Documentation: Professional documentation of cleaning processes, validation testing, and garment inspection that supports compliance with increasingly stringent Saudi occupational safety regulations.
- Capital Investment Avoidance: Elimination of substantial upfront investment in specialized equipment, facility modifications, and technical staffing required for establishing comparable in-house capabilities.
Industrial Laundry Services: Challenges
Organizations must also consider significant challenges when outsourcing workwear maintenance:
- Logistics Complexity: Required development of systematic collection, transportation, and redistribution processes that ensure clean garments are available when needed while minimizing operational disruption.
- Service Level Variability: Potential for inconsistent quality, particularly with providers serving multiple industries who may lack specialized protocols for specific contaminants relevant to particular industrial processes.
- Transport-Related Carbon Footprint: Environmental impact of regular transportation between facilities, particularly concerning in Saudi Arabia's urban industrial corridors where traffic congestion already presents environmental challenges.
- Emergency Response Limitations: Potential delays in addressing urgent cleaning needs that arise from unexpected contamination incidents or sudden increases in workwear requirements.
- Contract Dependency Risks: Vulnerability to service disruptions, price increases, or quality deterioration, particularly in regions where service provider options are limited.
In-House Care: Advantages
Maintaining workwear through internal facilities offers several compelling benefits:
- Process Control: Complete oversight of cleaning protocols, chemical selection, and quality verification, enabling precise alignment with specific industry requirements and organizational standards.
- Rapid Response Capability: Immediate availability for addressing unexpected contamination events, emergency cleaning requirements, or short-notice increases in workwear processing volume.
- Customized Treatment Options: Ability to develop specialized cleaning protocols tailored to specific materials, contaminants, and performance requirements unique to the organization's industrial processes.
- Reduced Handling and Transportation: Elimination of multiple touch points in the logistics chain, decreasing chances of garment damage, loss, or cross-contamination between facilities.
- Integration with Operations: Potential for seamless incorporation into existing operational workflows, particularly valuable in continuous manufacturing environments or facilities with specific shift patterns.
In-House Care: Challenges
Organizations considering in-house workwear maintenance must address significant obstacles:
- Substantial Initial Investment: Required capital allocation for specialized industrial washing equipment, water treatment systems, drying technologies, and facility modifications, typically ranging from 1.2-3.5 million SAR depending on capacity requirements.
- Technical Expertise Requirements: Necessary recruitment and retention of staff with specialized knowledge in industrial textile maintenance, chemical handling, and equipment operation—a challenging proposition in some Saudi industrial regions.
- Regulatory Compliance Burden: Direct responsibility for meeting wastewater discharge standards, chemical handling regulations, and occupational safety requirements associated with laundry operations.
- Space Allocation Challenges: Dedication of valuable facility space to non-core operations, particularly problematic in industrial zones where real estate carries premium costs.
- Utility Infrastructure Demands: Need for robust water supply, wastewater management, electrical capacity, and ventilation systems that may require significant facility modifications.
Comparative Cost Analysis
Understanding the true economic impact requires comprehensive analysis across multiple factors:
- Total Cost of Ownership: Comprehensive calculation reveals that in-house operations typically become cost-competitive only after processing 5,000+ garments weekly, with smaller operations generally experiencing 15-30% higher per-garment costs compared to outsourced services.
- Capital Expenditure vs. Operational Expense: Consideration of financial implications between substantial upfront investment (in-house) versus distributed operational expenses (outsourced), particularly significant for organizations with capital constraints.
- Staffing Impact Assessment: Analysis showing in-house operations typically requiring 1 dedicated staff member per 1,200-1,500 weekly garment capacity, representing significant ongoing labor expense often underestimated in initial projections.
- Hidden Cost Identification: Recognition of frequently overlooked expenses including maintenance contracts, technical training, compliance documentation, chemical inventory management, and quality control systems.
- Economies of Scale Thresholds: Research demonstrating that in-house operations generally require processing at least 70% of maximum capacity to achieve competitive per-garment costs compared to outsourced alternatives.
Quality and Performance Considerations
Workwear performance depends significantly on maintenance approach:
- Garment Integrity Impact: Testing demonstrating that specialized industrial processes can extend functional garment lifespan by 30-45% compared to conventional cleaning methods through reduced fabric stress and appropriate treatment of technical materials.
- Performance Features Preservation: Significant variation in maintenance of critical workwear attributes such as flame resistance, chemical repellency, high-visibility properties, and anti-static characteristics depending on processing methods and chemical selection.
- Contamination Management: Variable effectiveness in removing potentially hazardous substances, with specialized industrial providers typically achieving 96-99% removal rates for most common industrial contaminants versus 85-92% for general commercial processes.
- Quality Control Consistency: Consideration of inspection protocols, verification testing, and rejection criteria that ensure workwear continues to meet safety and performance specifications throughout its lifecycle.
- Documentation Standards: Assessment of record-keeping practices regarding cleaning verification, repair history, and performance testing that supports both regulatory compliance and internal quality assurance requirements.
Industry-Specific Considerations
Different industrial sectors present unique workwear maintenance challenges:
- Petrochemical Processing: Requirements for specialized hydrocarbon removal protocols, inherent flame resistance maintenance, and static electricity management that general laundry operations frequently cannot adequately address.
- Food Manufacturing: Necessity for validated sanitization processes, allergen removal protocols, and documentation supporting food safety compliance that demand specialized knowledge and equipment.
- Heavy Manufacturing: Challenges with metal particulate removal, lubricant extraction, and maintaining structural integrity of reinforced garments subject to extreme physical stress during use.
- Construction: Management of variable soil types, concrete dust, and building material residues that require adaptable cleaning approaches to prevent permanent garment damage.
- Mining and Extraction: Specialized requirements for removing deeply embedded mineral particulates, processing heavily soiled garments, and maintaining protective properties despite extreme contamination levels.
Compliance and Risk Management
Regulatory considerations significantly impact workwear maintenance decisions:
- Saudi Labor Law Requirements: Compliance with specific provisions regarding employer responsibilities for appropriate maintenance of provided protective equipment, including documentation of cleaning processes and effectiveness.
- International Standard Alignment: Adherence to industry-specific standards such as ISO 15797 (industrial laundering procedures), ISO 30023 (workwear performance after industrial processing), and ISO 14001 (environmental management systems).
- Cross-Contamination Prevention: Implementation of proper separation protocols ensuring contaminants from one work environment are not transferred to garments from different operational areas or facilities.
- Hazardous Waste Management: Proper handling of cleaning residues that may contain industrial chemicals, heavy metals, or other regulated substances requiring specialized disposal procedures.
- Documentation and Traceability: Maintenance of comprehensive records demonstrating regulatory compliance, particularly important during safety audits or following workplace incident investigations.
Environmental Sustainability Comparison
Each approach presents distinct environmental considerations:
- Water Consumption Efficiency: Industrial services typically achieve 40-60% greater water efficiency per garment through advanced recycling systems, continuous batch washers, and water recovery technologies compared to smaller in-house operations.
- Energy Utilization Optimization: Specialized providers generally demonstrate 25-35% lower energy consumption per processed garment through heat recovery systems, processing scale, and equipment optimization not economically feasible for most in-house facilities.
- Chemical Management: Professional industrial laundering typically utilizes 15-25% less cleaning chemistry per garment through precise dosing systems, formulation optimization, and recovery processes beyond the capabilities of standard in-house installations.
- Transportation Impact: Carbon emissions associated with regular garment transportation between facilities, representing an environmental cost not present with on-site processing that must be factored into overall sustainability assessment.
- Wastewater Treatment Capabilities: Specialized industrial laundry facilities generally implement advanced filtration, chemical treatment, and contaminant extraction systems exceeding those economically feasible for individual organizations.
Operational Integration Factors
Successful implementation depends on alignment with broader operations:
- Production Schedule Coordination: Development of maintenance cycles that synchronize with production shifts, ensuring clean workwear availability precisely when needed while minimizing excess inventory requirements.
- Inventory Management Systems: Implementation of tracking technologies (including RFID, barcode systems, or QR codes) that monitor individual garment location, cleaning history, and remaining lifecycle regardless of maintenance approach.
- Standard Operating Procedure Integration: Incorporation of workwear exchange protocols into existing operational procedures to ensure consistent implementation across shifts and departments.
- Emergency Response Protocols: Establishment of clearly defined procedures for addressing urgent cleaning requirements stemming from contamination incidents or unexpected operational changes.
- Change Management Considerations: Development of effective transition strategies when shifting between in-house and outsourced models, recognizing significant procedural and responsibility modifications required.
Worker Satisfaction Impact
Employee experience represents an often underestimated factor in maintenance model selection:
- Garment Comfort Factors: Considerable variation in wearer comfort based on cleaning approach, with research showing properly maintained workwear can reduce reported discomfort by 30-40% through better moisture management, reduced irritant residue, and fabric structure preservation.
- Health Perception Influence: Strong correlation between perceived cleaning effectiveness and worker confidence in health protection, with 65-75% of industrial employees reporting greater satisfaction when confident in decontamination processes.
- Availability and Access: Impact of maintenance model on consistent clean workwear availability, particularly important in operations requiring multiple daily changes or employing shift patterns that complicate distribution.
- Personal Responsibility Reduction: Elimination of unofficial at-home cleaning attempts that often compromise critical protective properties through inappropriate detergents, temperatures, or processes.
- Professional Appearance Pride: Connection between proper maintenance and garment appearance, with studies showing 55-70% of industrial workers report increased job satisfaction when wearing clean, properly maintained workwear.
Hybrid Model Considerations
Many Saudi organizations are finding value in combined approaches:
- Split Processing Strategy: Implementation of in-house capabilities for routine maintenance while outsourcing specialized decontamination, deep cleaning, or repair services requiring advanced equipment or expertise.
- Critical Item Prioritization: Development of multi-tier maintenance systems where safety-critical garments receive specialized processing while standard items follow more conventional maintenance paths.
- Seasonal Capacity Management: Utilization of external services during peak demand periods while maintaining baseline in-house capabilities for routine operations, particularly valuable in industries with significant seasonal variation.
- Progressive Implementation Approach: Phased development of in-house capabilities beginning with simple maintenance processes while continuing to outsource complex requirements until internal expertise and infrastructure mature.
- Geographic Distribution Solutions: Establishment of in-house facilities at major operational hubs while utilizing external services for remote locations where scale cannot justify dedicated capabilities.
Decision Framework for Saudi Organizations
Systematic evaluation should consider multiple organizational factors:
- Volume Threshold Analysis: Assessment of weekly workwear processing requirements against established breakeven points, recognizing that operations processing fewer than 3,500-4,000 garments weekly rarely achieve economic justification for comprehensive in-house facilities.
- Contamination Complexity Evaluation: Detailed analysis of specific soiling types, hazardous materials, and performance requirements to determine whether specialized expertise available through industrial services outweighs benefits of internal control.
- Geographic Service Availability: Consideration of industrial laundry service access in specific operational locations, particularly important for facilities in developing industrial regions where specialized providers may be limited.
- Capital Allocation Strategy Alignment: Assessment of whether substantial investment in non-core operations aligns with broader organizational financial strategy or whether capital preservation for primary business functions takes priority.
- Risk Profile Determination: Evaluation of the organization's tolerance for dependency on external providers versus preference for direct operational control, particularly important for critical operations where service disruption would create significant consequences.
Implementation Recommendations
Organizations can optimize results through structured approach:
- Comprehensive Baseline Assessment: Detailed documentation of current workwear inventory, cleaning requirements, maintenance cycles, and performance expectations before selecting either approach.
- Piloted Implementation: Structured testing of proposed maintenance model with representative garment selection and comprehensive performance evaluation before full-scale commitment.
- Defined Performance Metrics: Establishment of specific, measurable quality indicators including cleanliness validation, protective property retention, processing turnaround time, and garment longevity.
- Staff Training Programs: Development of appropriate education for employees regarding proper workwear handling, collection procedures, and performance expectations regardless of maintenance model selected.
- Regular Evaluation Protocol: Implementation of scheduled assessment processes reviewing both technical performance and economic efficiency of the selected maintenance approach, with willingness to adjust as organizational needs evolve.
Future Trends Affecting Decision-Making
Emerging developments will influence workwear maintenance strategies:
- Smart Textile Integration: Increasing incorporation of electronic monitoring components, conductive elements, and embedded sensors in industrial workwear requiring specialized maintenance protocols beyond conventional cleaning capabilities.
- Environmental Regulation Evolution: Anticipated strengthening of Saudi environmental standards regarding water usage, chemical discharge, and energy efficiency that will increase compliance complexity for in-house operations.
- Automated Processing Advancement: Continuing development of robotic handling systems, AI-driven inspection technologies, and automated processing equipment that may reduce the labor advantage traditionally held by external service providers.
- Supply Chain Localization: Emerging Saudi providers offering specialized industrial laundering capabilities in previously underserved regions as part of broader industrial ecosystem development.
- Chemical Innovation Impact: Development of next-generation cleaning chemistries specifically engineered for advanced technical textiles, potentially altering the expertise and equipment requirements for effective maintenance.
Conclusion: Strategic Decision Beyond Simple Outsourcing
The evaluation between industrial laundry services and in-house care represents far more than a simple outsourcing consideration. For Saudi industrial operations, this decision touches critical aspects of operational efficiency, regulatory compliance, environmental responsibility, worker welfare, and financial resource allocation.
The optimal approach emerges from rigorous analysis of organizational specifics rather than general industry trends. Progressive organizations recognize that workwear maintenance represents an integral component of their overall operational and safety systems—one deserving thorough consideration beyond immediate cost comparisons. Whether selecting specialized external partners or developing internal capabilities, successful implementation requires ongoing commitment to quality standards that ensure workwear continues to protect employees while supporting operational excellence.