Industrial Laundry Services for Work Uniforms in Saudi Arabia
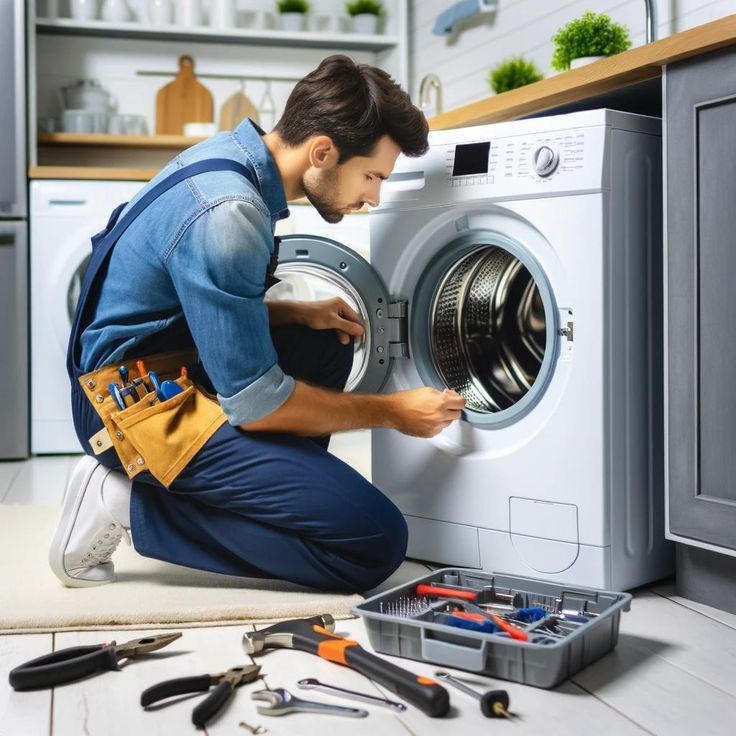
In Saudi Arabia's rapidly evolving industrial landscape, the management of work uniform cleanliness and maintenance has emerged as a critical operational component with significant implications for workplace safety, employee satisfaction, and corporate sustainability objectives. As the Kingdom continues its ambitious economic transformation through Vision 2030 initiatives, industrial laundry services have developed into sophisticated operations delivering specialized solutions far beyond basic cleaning—addressing the unique requirements of diverse sectors from petrochemical processing to food manufacturing.
Strategic Value of Specialized Uniform Processing
Professional industrial laundry services deliver measurable benefits across multiple business dimensions:
- Regulatory Compliance Assurance: Saudi industrial operations face increasingly stringent workplace safety regulations, with specialized laundry services implementing validated processes ensuring complete removal of hazardous contaminants including hydrocarbons, heavy metals, and chemical residues—providing documented compliance verification increasingly required by regulatory authorities.
- Protective Performance Maintenance: Safety garment functionality depends on proper processing, with specialized industrial laundry providers implementing technical protocols preserving critical protective properties including flame resistance, chemical repellency, and high-visibility characteristics—maintaining life-saving functionality that improper handling would compromise.
- Operational Efficiency Enhancement: Outsourced processing delivers significant productivity benefits, with Saudi industrial operations reporting 15-22% reduction in uniform-related administrative burden and 30-40% decrease in garment replacement frequency through professional maintenance—allowing operational personnel to focus on core responsibilities rather than clothing management.
- Cross-Contamination Prevention: Specialized facilities implement critical separation protocols, with comprehensive systems preventing hazardous substance transfer between garments from different industrial environments—addressing significant workplace safety risks impossible to manage through conventional cleaning approaches.
- Environmental Compliance Management: Waste handling regulations create significant responsibilities, with professional industrial laundry providers implementing permitted treatment systems for contaminated wastewater and hazardous residues—addressing environmental compliance requirements beyond the capabilities of most industrial operations to manage independently.
Industry-Specific Processing Requirements
Different sectors require specialized laundry approaches addressing unique challenges:
- Petrochemical Industry Protocols: Oil and gas operations create distinctive contamination profiles, with specialized laundry services implementing hydrocarbon-specific pre-treatment processes, engineered detergent formulations, and validated temperature cycles—addressing both visible soiling and molecular-level contamination while preserving FR garment properties critical for worker safety.
- Food Processing Standards: Consumable production environments require stringent hygiene, with dedicated laundry services implementing food-safety protocols including sanitization cycles achieving 5-log pathogen reduction, allergen-specific treatment processes, and segregated handling preventing cross-contamination—meeting SFDA requirements while extending garment longevity.
- Healthcare Textile Management: Medical environments present unique challenges, with specialized services implementing validated disinfection processes, sterile packaging options for critical applications, and bioburden reduction treatments—addressing infection control requirements while maintaining comfort properties essential for clinical staff performing extended procedures.
- Heavy Manufacturing Solutions: Metal fabrication and industrial production create intense soiling challenges, with effective laundry services implementing specialized pre-treatment systems addressing embedded metal particulates, lubricant contamination, and industrial adhesives—restoring both appearance and functionality while preventing cross-contamination to other garment categories.
- Construction Sector Approaches: Building industry workwear faces unique demands, with appropriate processing implementing reinforced mechanical action for cement compound removal, specialized treatments addressing bituminous contamination, and enhanced structural inspection—extending garment longevity in applications facing extreme physical challenges beyond typical industrial exposure.
Technical Process Components
Advanced industrial laundry operations implement sophisticated multi-stage systems:
- Contamination Assessment Technology: Modern facilities implement advanced evaluation systems, with leading Saudi industrial laundry providers utilizing spectroscopic analysis, fluorescent detection systems, and contamination mapping technologies—enabling precise treatment customization based on specific soiling profiles rather than generic processing assumptions.
- Pre-Treatment Specialization: Effective processing begins with targeted preparation, with comprehensive systems implementing contaminant-specific pre-spotting, specialized emulsification processes for petroleum compounds, and appropriate neutralization treatments for chemical residues—addressing specific challenges before main washing to enhance removal effectiveness while reducing fabric stress.
- Wash Chemistry Engineering: Formula development represents critical expertise, with advanced providers utilizing chemical engineering approaches developing specific detergent combinations, pH-controlled processing sequences, and specialized surfactant systems—creating targeted solutions addressing specific industrial contaminants while preserving garment functional properties.
- Temperature Profile Management: Thermal control significantly impacts both cleaning efficacy and garment longevity, with sophisticated operations implementing precise temperature staging, controlled gradients, and application-specific maximum settings—balancing contaminant removal requirements against potential heat damage to specialized fabrics and reflective elements.
- Mechanical Action Calibration: Physical agitation requires careful optimization, with advanced systems precisely controlling rotation patterns, acceleration profiles, and dwell periods—removing stubborn contaminants while minimizing fabric stress, seam damage, and premature wear that would reduce garment service life and protective functionality.
Quality Control Systems
Maintaining consistent processing standards requires structured oversight approaches:
- Multi-Stage Inspection Protocols: Comprehensive quality verification requires systematic processes, with effective industrial laundry operations implementing structured assessment at key production stages including pre-wash sorting, post-wash evaluation, finishing inspection, and final verification—creating multiple detection opportunities for quality issues requiring intervention.
- Contamination Verification Technology: Residue detection ensures safety compliance, with advanced facilities utilizing specialized testing including chemical indicator systems, UV detection methods, and in some cases portable spectrometry—providing objective verification that hazardous substances have been completely removed rather than relying on visual inspection alone.
- Functional Property Validation: Performance characteristics require specific verification, with thorough providers implementing regular testing of critical protective properties including flame resistance retention, water repellency assessment, and retroreflective performance measurement—ensuring life-safety features remain fully functional throughout garment lifecycle.
- Statistical Process Control: Consistent quality requires systematic monitoring, with sophisticated operations implementing data-driven oversight including trend analysis, variance monitoring, and statistical sampling protocols—identifying potential process drift before quality issues impact customer operations or worker safety.
- Compliance Documentation Systems: Regulatory requirements increasingly demand verification, with comprehensive industrial laundry services providing detailed processing certification, contaminant removal confirmation, and chain-of-custody tracking—creating defensible compliance evidence increasingly required by Saudi regulatory authorities and international certification bodies.
Specialized Equipment Technology
Advanced industrial laundry operations utilize purpose-designed systems:
- Barrier Washing Architecture: Contamination control requires physical separation, with advanced facilities implementing pass-through barrier systems creating complete isolation between soiled garment handling and clean processing areas—preventing recontamination while supporting unidirectional workflow enhancing both efficiency and hygiene.
- Water Recycling Systems: Resource conservation drives technology adoption, with leading Saudi industrial laundry operations implementing multi-stage water reclamation systems capturing, filtering, and reusing process water—simultaneously addressing sustainability objectives and operational cost management in the Kingdom's water-constrained environment.
- Specialized Dryer Technology: Thermal finishing significantly impacts both quality and efficiency, with advanced operations utilizing precision moisture detection, controlled airflow systems, and garment-specific temperature profiling—optimizing energy consumption while preventing heat damage to specialized fabrics, reflective elements, and synthetic components.
- Automated Garment Handling: Labor efficiency drives system development, with sophisticated facilities implementing conveyor-based transport systems, automated sorting technologies, and robotic folding equipment—reducing manual handling while improving throughput capacity, processing consistency, and workplace ergonomics.
- Energy Recovery Integration: Operational sustainability requires system optimization, with progressive Saudi laundry operations implementing heat reclamation technology, process water energy transfer, and thermal cascade systems—capturing and reusing energy that conventional systems would waste while reducing both environmental impact and operating costs.
Contamination Management Approaches
Handling hazardous substances requires specialized protocols:
- Substance-Specific Isolation: Cross-contamination prevention requires systematic separation, with effective industrial laundry services implementing comprehensive sorting systems segregating garments by contaminant category—preventing dangerous chemical interactions while enabling targeted treatment approaches optimized for specific substance removal.
- Hydrocarbon Processing Specialization: Petroleum compounds present unique challenges, with specialized providers implementing solvent-assisted pre-treatment, engineered emulsification systems, and appropriate surfactant combinations—achieving complete removal of both light and heavy petroleum fractions while preserving fabric integrity and FR performance.
- Heavy Metal Remediation: Metallic contamination requires targeted approaches, with advanced operations implementing chelation chemistry, specialized sequestering agents, and appropriate pH management—addressing potentially toxic metal compounds while preventing redeposition that would compromise both appearance and safety.
- Chemical Residue Neutralization: Industrial compounds require specific countermeasures, with comprehensive processing systems implementing appropriate neutralization chemistry, reactive agent treatment, and verification testing—ensuring complete deactivation of potentially harmful substances before garment return to workplace environments.
- Biological Contamination Control: Microbial hazards demand validated processes, with thorough industrial laundry services implementing thermal disinfection protocols, antimicrobial chemistry applications, and bioburden testing—addressing potential pathogen exposure particularly critical in food processing, pharmaceutical, and healthcare adjacent industrial operations.
Service Model Options
Industrial operations can access laundry services through various arrangements:
- Rental-Processing Integration: Combined programs offer operational simplicity, with comprehensive service providers delivering complete uniform management including garment provision, regular processing, inventory management, and automatic replacement—converting what would be capital investment and management complexity into straightforward operational expense with predictable budgeting.
- Customer-Owned Goods Processing: Ownership with external cleaning provides balanced control, with specialized services processing company-purchased garments through regular collection and delivery cycles—enabling greater uniform customization and potential long-term cost advantages while eliminating processing infrastructure requirements and regulatory compliance burdens.
- On-Premises Processing Support: Some operations maintain internal facilities, with industrial laundry specialists providing chemical supply, equipment maintenance, process development, and technical support—enabling operational independence while benefiting from specialized expertise difficult to maintain within most industrial organizations.
- Hybrid System Implementation: Combined approaches offer strategic advantages, with some Saudi industrial operations implementing mixed models processing standard items through external services while handling specialized or security-sensitive garments through limited internal facilities—optimizing both operational efficiency and control where specifically required.
- Emergency Response Capability: Contingency planning requires backup systems, with comprehensive service providers offering rapid-response options addressing unexpected contamination events, processing system failures, or surge requirements—providing business continuity protection beyond regular processing arrangements.
Garment Tracking and Management
Inventory control systems ensure accountability and efficiency:
- RFID Implementation: Electronic identification transforms management capabilities, with advanced Saudi industrial laundry operations implementing comprehensive RFID systems enabling individual garment tracking, automated sorting, usage pattern analysis, and lifecycle management—creating unprecedented visibility while virtually eliminating loss-related costs.
- Barcode Control Systems: Optical identification provides cost-effective tracking, with established services utilizing barcode technologies supporting basic inventory management, simple usage tracking, and streamlined distribution—delivering core management capabilities with lower implementation costs suitable for smaller operations or less complex requirements.
- Individual Assignment Tracking: Accountability systems enhance compliance, with comprehensive services implementing user-specific assignment records, usage history tracking, and individual responsibility documentation—supporting both cost allocation and regulatory compliance particularly important in hazardous substance environments requiring exposure monitoring.
- Wear Pattern Analysis: Usage data enables optimization, with sophisticated systems monitoring garment lifecycle patterns, identifying abnormal wear indicators, and analyzing replacement frequency by work area—providing actionable intelligence supporting both improved garment specification and potential workplace process modifications addressing root causes of excessive uniform damage.
- Mobile Application Integration: User interfaces enhance service accessibility, with progressive providers developing smartphone-based systems enabling simple uniform requests, issue reporting, delivery tracking, and usage management—improving service responsiveness while reducing administrative burden on both industrial clients and service operations.
Logistical System Requirements
Physical movement of garments requires specialized approaches:
- Contamination-Safe Transport: Hazardous substance management extends to logistics, with comprehensive industrial laundry services implementing specialized collection systems including substance-specific containment bags, sealed transport containers, and appropriate vehicle segregation—preventing environmental exposure during movement between client operations and processing facilities.
- Route Optimization Technology: Efficiency requires systematic planning, with advanced providers implementing AI-driven route development, dynamic scheduling systems, and real-time adjustment capabilities—maximizing service reliability while minimizing both transportation costs and environmental impact through reduced fuel consumption.
- Cross-Contamination Prevention: Vehicle management requires careful protocols, with effective services implementing structured loading arrangements, appropriate barrier systems, and dedicated transport options for high-risk environments—preventing dangerous substance transfer between industrial clients operating with incompatible contaminants.
- Remote Site Servicing: Saudi Arabia's industrial geography creates unique challenges, with specialized providers developing appropriate capabilities for distant operations including extended logistics networks, potential on-site processing for remote locations, and appropriate inventory management addressing transportation timeline realities.
- Delivery System Options: Distribution approaches affect operational efficiency, with service customization including direct-to-employee distribution, locker system deployment, or centralized uniform room delivery—aligning with specific client operational structures while ensuring efficient garment availability when and where needed.
Cost Management Strategies
Optimizing uniform processing economics requires structured approaches:
- Volume Consolidation Benefits: Scale significantly impacts pricing, with multi-site Saudi industrial operations increasingly implementing enterprise agreements consolidating volume across locations—leveraging combined scale to secure preferential pricing while standardizing service levels and compliance approaches across organizational operations.
- Garment Standardization Advantages: Specification consistency creates efficiency opportunities, with strategic uniform programs developing standardized garment platforms across multiple departments or functions where appropriate—reducing processing complexity while creating inventory flexibility addressing staffing fluctuations or departmental changes.
- Lifecycle Extension Focus: Longevity significantly impacts program economics, with comprehensive industrial laundry services implementing garment-specific processing optimized for maximum useful life—potentially increasing initial processing costs but delivering substantial total cost advantages through reduced replacement frequency and extended amortization periods.
- Soil Classification Implementation: Processing customization improves efficiency, with sophisticated programs developing tiered systems addressing different contamination levels with appropriate intensity—applying enhanced processing only where specifically required rather than subjecting all garments to maximum treatment regardless of actual need.
- Transport Efficiency Optimization: Collection frequency affects both service cost and inventory requirements, with balanced programs establishing appropriate schedule optimization—finding optimal balance between minimizing transportation expense and maintaining appropriate garment float inventory supporting operational requirements.
Sustainability Considerations
Environmental responsibility increasingly influences service selection:
- Water Conservation Technology: Resource management drives innovation, with leading Saudi industrial laundry operations implementing advanced conservation systems achieving 75-85% water recycling rates through multi-stage filtration, biological treatment, and appropriate quality monitoring—dramatically reducing consumption of the Kingdom's scarce water resources compared to conventional processing or on-premises alternatives.
- Energy Efficiency Implementation: Carbon reduction supports national objectives, with progressive service providers developing comprehensive efficiency programs including heat recovery systems, variable frequency drives, process optimization, and renewable energy integration—aligning with Saudi Vision 2030 sustainability goals while reducing operational costs.
- Chemical Usage Optimization: Formulation engineering enhances environmental performance, with advanced providers implementing precision dosing systems, biodegradable chemistry selection, and concentrated product utilization—reducing both environmental impact and chemical expense while maintaining or improving cleaning effectiveness.
- Wastewater Management Excellence: Discharge quality affects compliance position, with responsible industrial laundry operations implementing comprehensive treatment systems addressing both regulated parameters and emerging contaminants of concern—exceeding regulatory requirements while protecting Saudi Arabia's sensitive receiving environments.
- Transportation Impact Reduction: Logistics optimization supports carbon objectives, with efficient providers implementing route optimization, vehicle modernization, alternative fuel adoption where feasible, and appropriate maintenance programs—minimizing transportation-related environmental impact within service delivery requirements.
Provider Selection Criteria
Choosing appropriate service partners requires systematic evaluation:
- Technical Capability Assessment: Processing expertise varies significantly, with thorough evaluation requiring detailed review of contamination management capabilities, specialized chemistry applications, protective property preservation processes, and quality control systems—identifying providers with specific expertise matching particular industrial operation requirements.
- Compliance Verification Systems: Regulatory alignment requires documented processes, with effective assessment examining provider certification status, environmental permits, waste management protocols, and processing validation methods—ensuring selected partners maintain appropriate compliance positioning protecting industrial clients from potential liability exposure.
- Capacity Adequacy Evaluation: Service reliability depends on appropriate scale, with prudent selection processes verifying processing capacity, equipment redundancy, peak handling capability, and appropriate contingency planning—preventing service disruption that could impact industrial operations through uniform availability limitations.
- Financial Stability Analysis: Partnership sustainability requires provider viability, with thorough evaluation examining service company financial position, investment history, organizational stability, and market positioning—identifying partners capable of maintaining service continuity through long-term relationships rather than creating potential disruption through financial instability.
- Technology Investment History: Forward capability often reflects past patterns, with strategic selection processes reviewing provider modernization history, technology adoption approaches, and innovation implementation—identifying partners demonstrating commitment to continuous improvement rather than maintaining minimal capability adequate only for current requirements.
Contract Structuring Approaches
Effective agreements address critical operational and financial factors:
- Performance Specification Development: Service expectations require explicit documentation, with comprehensive agreements establishing specific requirements for processing quality, turnaround time, garment longevity, and contamination management—creating clear accountability frameworks rather than generalized service promises subject to interpretation.
- Volume Commitment Balancing: Quantity guarantees affect pricing structures, with optimal contracts establishing appropriate balance between provider volume certainty and industrial operation flexibility—typically implementing tiered pricing systems accommodating reasonable fluctuation while maintaining economic sustainability for both parties.
- Term Optimization Strategy: Duration decisions balance competing objectives, with most effective Saudi industrial service agreements establishing 2-3 year initial terms providing rate stability while including structured performance reviews and specific termination provisions protecting operational flexibility if service proves inadequate.
- Price Adjustment Mechanisms: Long-term agreements require change provisions, with well-constructed contracts implementing appropriate escalation formulas tied to objective indicators including published cost indexes, documented commodity pricing, or other transparent benchmarks—providing predictability while ensuring economic sustainability as underlying cost structures evolve.
- Damage Assessment Protocols: Garment condition disputes require resolution frameworks, with effective agreements establishing clear definitions of normal wear versus excessive damage, specific evaluation procedures, and fair allocation of replacement costs—preventing adversarial relationships while creating appropriate incentives for both proper processing and reasonable garment care.
Implementation Best Practices
Successful program deployment requires structured transition management:
- Process Mapping Integration: Operational alignment ensures seamless service, with effective implementation beginning through detailed workflow analysis addressing collection timing, processing requirements, delivery scheduling, and inventory management—creating synchronized systems rather than forcing industrial operations to adapt around service provider limitations.
- Soil Survey Development: Contamination profiling enhances processing effectiveness, with thorough programs conducting comprehensive analysis of specific workplace substances, concentration patterns, and exposure variations across different positions—enabling targeted processing design rather than generic approaches inadequate for specialized industrial environments.
- Garment Specification Review: Uniform compatibility affects processing success, with prudent implementation including detailed evaluation of existing garments addressing fabric composition, construction methods, and specialized features—identifying potential processing challenges before implementation while enabling appropriate technique modification or garment specification adjustments where necessary.
- Phased Transition Planning: Operational continuity requires careful changeover, with successful implementations typically utilizing staged approaches transitioning departments sequentially rather than attempting complete conversion simultaneously—allowing process refinement while minimizing potential disruption to industrial operations.
- Staff Education Integration: User cooperation enhances program success, with comprehensive implementation including specific communication addressing proper uniform handling, appropriate collection procedures, contamination segregation requirements, and issue reporting processes—creating partnership approach rather than simply imposing new systems without adequate explanation.
Performance Monitoring Systems
Ensuring ongoing service quality requires structured oversight approaches:
- Key Performance Indicator Development: Measurement enables management, with effective oversight systems establishing specific metrics addressing processing quality, turnaround consistency, garment longevity, and service responsiveness—creating objective evaluation framework beyond subjective assessment or anecdotal feedback.
- Regular Review Implementation: Structured evaluation prevents service drift, with successful programs implementing scheduled assessment meetings reviewing performance data, addressing emerging concerns, and identifying improvement opportunities—maintaining service focus while preventing small issues from developing into significant problems.
- Contamination Testing Programs: Safety verification requires objective assessment, with thorough monitoring systems implementing regular testing of processed garments verifying complete removal of workplace substances—providing documented evidence supporting both regulatory compliance and worker protection beyond visual inspection alone.
- Cost Trend Analysis: Economic performance requires systematic tracking, with comprehensive programs monitoring key indicators including per-garment processing costs, replacement frequency patterns, and program administration expenses—identifying optimization opportunities while ensuring ongoing alignment with budgetary expectations.
- Continuous Improvement Integration: Evolution prevents stagnation, with progressive oversight approaches incorporating structured development processes identifying enhancement opportunities, testing potential modifications, and implementing validated improvements—creating dynamic programs evolving alongside changing industrial requirements rather than static services failing to address emerging needs.
Emerging Technologies
Forward-looking operations increasingly incorporate innovative approaches:
- Advanced Polymer Formulations: Chemistry innovation enhances performance, with cutting-edge providers implementing specialized detergent systems incorporating engineered polymers, targeted surfactant combinations, and application-specific enzymes—achieving superior cleaning results with reduced environmental impact compared to conventional chemistry approaches.
- Ultrasonic Enhancement Systems: Physical cleaning augmentation improves results, with innovative facilities implementing frequency-optimized ultrasonic systems creating microscopic cavitation effects—dislodging embedded contaminants from fabric structures while reducing both chemical requirements and mechanical wear compared to conventional agitation alone.
- Near-Waterless Processing: Resource conservation drives development, with pioneering Saudi industrial laundry operations implementing CO₂-based cleaning systems, advanced vapor technologies, or other alternative processing methods—dramatically reducing water consumption while achieving equivalent or superior cleaning results for appropriate garment categories.
- Artificial Intelligence Integration: Data utilization enhances optimization, with sophisticated providers implementing machine learning systems analyzing processing patterns, predicting maintenance requirements, and continuously refining operational parameters—creating self-improving systems delivering superior results while reducing resource consumption through continuous optimization.
- Blockchain Verification Systems: Compliance documentation benefits from enhanced security, with advanced providers developing distributed ledger approaches creating immutable processing records, verifiable contamination testing results, and secure chain-of-custody documentation—supporting regulatory compliance with tamper-proof verification increasingly valuable in highly regulated industrial environments.
Case Study: Petrochemical Processing Implementation
A major Saudi petrochemical operation with 1,200 employees implemented a comprehensive industrial laundry service program addressing significant hydrocarbon contamination challenges, revealing instructive insights regarding specialized processing requirements in high-hazard environments.
Initial assessment identified critical challenges including heavy crude oil contamination, aromatic hydrocarbon exposure, and catalyst material residues—requiring specialized processing beyond conventional industrial laundry capabilities. The operation developed comprehensive specifications addressing both contaminant removal requirements and FR garment preservation needs, with particular emphasis on documented verification supporting both worker safety and regulatory compliance objectives.
The resulting program utilized a specialized industrial laundry provider with petroleum industry expertise, implementing a custom processing system including solvent pre-treatment stages, engineered surfactant formulations, and controlled temperature profiles specifically designed for complete hydrocarbon removal while preserving critical FR properties. Comprehensive tracking systems utilizing RFID technology created complete processing documentation while enabling exposure monitoring for employees working in various facility areas.
Most significantly, post-implementation analysis demonstrated measurable improvements across multiple objectives: achieving 100% verification of contaminant removal, extending average FR garment lifespan by 34% through specialized processing, and reducing overall program costs by 22% compared to previous approaches—while simultaneously improving environmental performance through advanced water recycling and waste management systems.
The implementation demonstrated the critical importance of specialized expertise in addressing complex industrial contamination challenges, with generic processing approaches proving inadequate for the specific technical requirements of high-hazard petrochemical environments where both worker safety and environmental compliance demand specialized solutions beyond conventional capabilities.
Conclusion: Beyond Basic Garment Processing
As Saudi Arabia's industrial sector continues its remarkable development through Vision 2030 initiatives, uniform processing increasingly represents a specialized technical discipline rather than simple garment cleaning. The most successful Saudi industrial operations recognize that appropriate laundry services deliver value far beyond basic cleanliness—addressing critical requirements spanning worker protection, regulatory compliance, environmental responsibility, and operational efficiency.
By implementing comprehensive approaches addressing both technical processing requirements and strategic business objectives, forward-thinking Saudi industrial leaders transform what could be merely administrative functions into valuable operational assets. When properly conceptualized and executed with appropriate attention to specific industrial requirements, specialized uniform processing services deliver measurable business benefits while enhancing both worker safety and environmental performance in the Kingdom's dynamic industrial landscape.