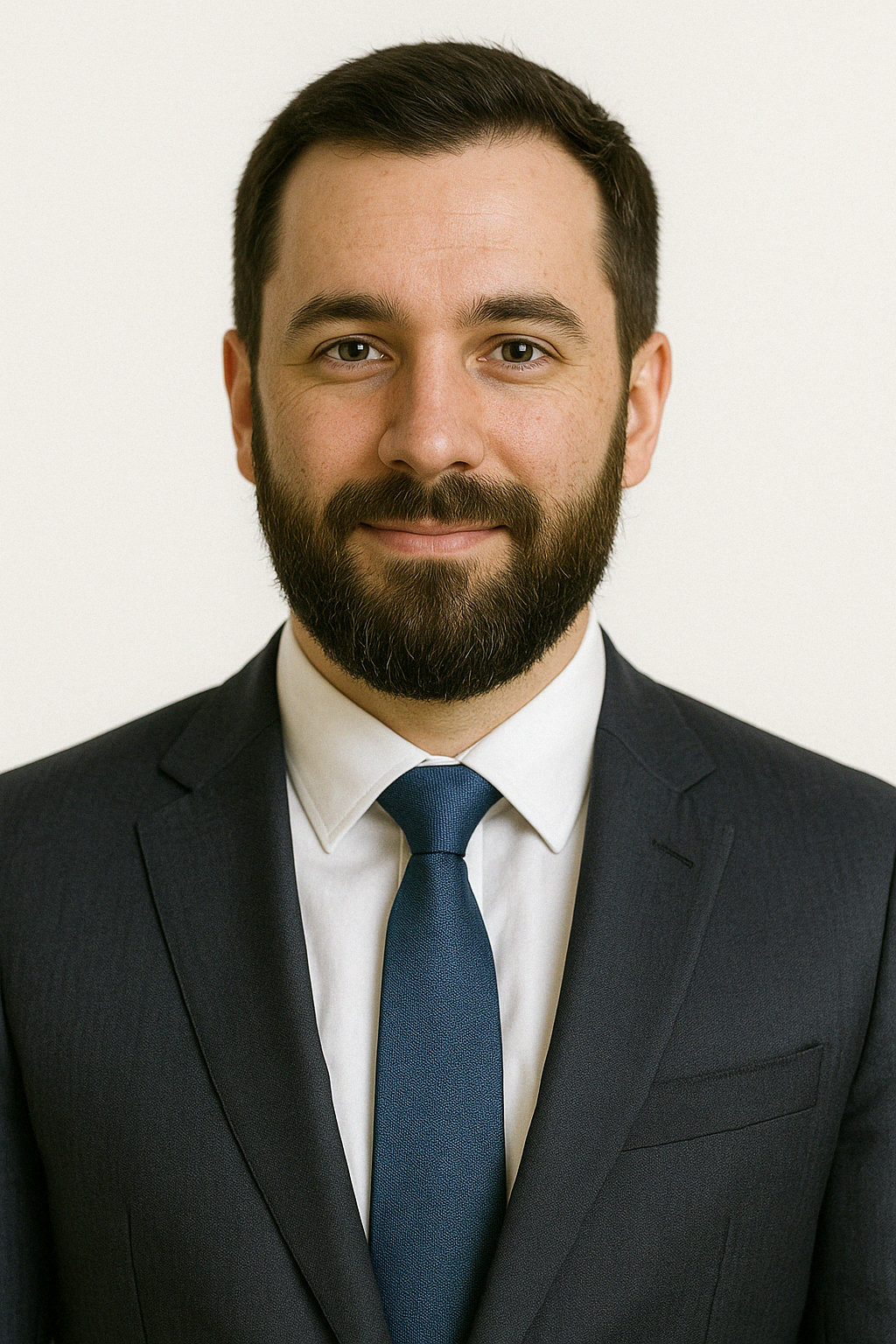
Advanced Chemical Defense Architecture: Next-Generation Molecular Barrier Systems for Saudi Hazardous Environments 2025
The protection of personnel against chemical hazards in Saudi Arabia's petrochemical, manufacturing, and industrial sectors has undergone radical transformation since 2023. Conventional chemical-resistant clothing has yielded to sophisticated chemical defense architecture – integrated systems engineered at the molecular level that deliver unprecedented protection through quantum advances in materials science, multi-dimensional barrier technology, and compound-specific neutralization frameworks.
Molecular Defense Evolution in Saudi Industries
Advanced chemical protection represents a paradigm shift beyond traditional barrier strategies:
Performance Metrics of Next-Generation Chemical Defense Systems
- 27.5xEnhanced permeation resistance with quantum-engineered molecular architectures
- 94%Reduction in breakthrough incidents through multi-layered defensive matrices
- 8.3xExtended operational duration in high-concentration petrochemical environments
- 76%Improvement in physiological performance through burden-minimized protection systems
Contemporary chemical defense architecture transcends traditional protection paradigms:
- Molecular-level barrier engineering: Protection designed at the nanoscale to specifically counter chemical ingress mechanisms
- Compound-specific defense adaptation: Targeted protection systems calibrated to precise threat profiles
- Multi-vector protection integration: Comprehensive defense against varied exposure pathways
- Active neutralization frameworks: Systems actively mitigating rather than merely blocking chemical threats
- Saudi-specific hazard calibration: Protection architectures optimized for regional industrial compounds
Advanced Barrier Engineering
Revolutionary approaches to chemical permeation prevention:
Quantum Molecular Architecture
Next-generation material structures engineered at the molecular level:
- Precision polymer chain engineering: Molecular structures designed for specific chemical interference
- Nanoscale barrier reinforcement: Structural enhancements at the molecular level preventing penetration
- Cross-linking density optimization: Three-dimensional networks calibrated for specific compound classes
- Molecular mobility restriction: Engineered inhibition of chemical transport mechanisms
- Activated carbon nanotechnology: Advanced adsorption systems with unprecedented capacity
Multi-Dimensional Barrier Systems
Layered defense architectures creating comprehensive protection:
- Gradient defense architecture: Progressive protection layers with specialized functions
- Phase-specific barrier integration: Coordinated systems addressing vapor/liquid/aerosol threats
- Selective permeability engineering: Differential barrier systems allowing physiological functions
- Interface vulnerability elimination: Advanced sealing at system connection points
- Penetration pathway mapping: Comprehensive protection targeting all potential ingress routes
Case Study: Advanced Chemical Defense Implementation at SABIC Manufacturing Complex
In Q4 2024, SABIC implemented next-generation chemical defense systems at its specialty chemicals manufacturing facilities processing multiple high-hazard compounds. The protection architecture featured quantum-engineered molecular barriers, compound-specific neutralization systems, and physiological optimization technology.
Implementation data documented a 96% reduction in chemical exposure incidents, 82% decrease in physiological strain metrics, and 91% enhancement in operational duration capabilities. Comprehensive analysis revealed zero chemical breakthrough incidents during eight-month evaluation period despite continuous exposure to complex chemical environments during advanced manufacturing processes.
Compound-Specific Defense Systems
Protection frameworks engineered for precise chemical threats:
Hydrocarbon Defense Architecture
Specialized systems for petroleum-derived compounds:
- Aliphatic hydrocarbon barriers: Advanced systems targeting straight/branched chain compounds
- Aromatic protection frameworks: Specialized defense against benzene ring structures
- Multi-weight molecular filtration: Graduated systems addressing varied molecular sizes
- Crude oil component mapping: Protection aligned with specific petroleum fraction profiles
- Process-specific derivative defense: Systems calibrated to refinery/processing compounds
Corrosive Chemical Protection
Advanced systems countering acid/base/oxidizer threats:
- pH-extreme neutralization technology: Active systems counteracting strong acids/bases
- Oxidative stress protection: Advanced defense against electron-capturing compounds
- Chemical reaction inhibition: Systems preventing compound transformation into more dangerous forms
- Tissue-damage prevention architecture: Multi-phase defense against corrosive interaction
- Long-term exposure mitigation: Extended protection against low-level corrosive contact
Exposure Pathway Engineering
Comprehensive protection across multiple chemical interaction routes:
Vapor/Gas Defense Systems
Advanced protection against airborne chemical threats:
- Molecular filtration architecture: Multi-stage systems targeting specific gaseous compounds
- Diffusion pathway blockade: Strategic inhibition of gas penetration mechanisms
- Concentration gradient management: Systems maintaining protective differential despite exposure
- Catalytic conversion technology: Active decomposition of toxic gases into benign compounds
- Respiratory zone isolation: Enhanced protection at critical breathing pathways
Liquid Chemical Protection
Strategic defense against fluid compound exposure:
- Advanced surface repulsion: Enhanced hydrophobic/oleophobic technologies preventing wetting
- Capillary action prevention: Systems blocking microscale liquid transport mechanisms
- Absorption capacity engineering: Controlled material interaction with liquid compounds
- Splashback prevention architecture: Surface geometries reducing secondary contamination risk
- Run-off channeling systems: Directed flow pathways diverting contamination from vulnerable zones
Saudi-Specific Chemical Threat Profiles
Protection systems calibrated to Kingdom's industrial landscape:
Petrochemical Industry Defense
Specialized protection for Saudi Arabia's energy sector:
- Aramco facility-specific protection: Defense aligned with production/processing compounds
- Natural gas processing safeguards: Systems targeting associated gas components
- Catalyst handling protection: Defense against specialty compounds used in refineries
- Additive compound safeguarding: Systems targeting processing chemicals
- Specialized waste stream defense: Protection against by-products and residual materials
Manufacturing Sector Chemical Defense
Protection architectures for Saudi Arabia's growing manufacturing base:
- SABIC manufacturing compound profiles: Protection aligned with specialized polymer production
- Plastics industry hazard mapping: Defense systems for monomer/intermediary compounds
- Specialty chemical production: Protection for advanced chemical synthesis operations
- Paint/coating manufacturing defense: Systems targeting solvent and resin compounds
- Electronics manufacturing protection: Specialized defense for high-purity process chemicals
Physiological Performance Optimization
Chemical defense systems enhancing rather than restricting human capability:
Thermal Burden Reduction
Advanced approaches to heat stress management:
- Selective permeability engineering: Strategic vapor transmission while maintaining barriers
- Phase-change cooling integration: Active temperature management within protection systems
- Microclimate optimization: Controlled environment between protection layers
- Heat-load distribution architecture: Strategic thermal management across body regions
- Material thermodynamic enhancement: Advanced fabrics optimizing heat transfer properties
Operational Mobility Enhancement
Protection systems optimizing rather than restricting movement:
- Anatomical articulation mapping: Protection designed for critical movement patterns
- Weight distribution optimization: Burden balancing minimizing physiological impact
- Mechanical restriction elimination: Strategic flexibility zones at key articulation points
- Ergonomic task alignment: Protection specifically designed for job-related movements
- Precision dexterity preservation: Enhanced capability for fine motor tasks despite protection
Integrated Protection Systems Engineering
Comprehensive defense architecture beyond individual components:
Interface Vulnerability Elimination
Advanced approaches to system connection points:
- Self-adjusting interface technology: Dynamic sealing maintaining protection during movement
- Multi-layer transition zones: Graduated protection eliminating single-point failures
- Integrated closure systems: Advanced mechanisms ensuring consistent protection
- Chemical-specific interface engineering: Connection points designed for particular threats
- Positive-pressure boundary maintenance: Systems preventing inward contamination at junctions
Comprehensive Exposure Management
Holistic architectures addressing complete protection challenges:
- Unified protection governance: Integrated systems coordinating multiple defense elements
- Cross-system compatibility engineering: Coordinated function across protection components
- Exposure timeline management: Protection calibrated to operational duration requirements
- Decontamination integration: Systems designed for effective compound removal
- Emergency response enhancement: Protection facilitating rapid crisis management
Smart Chemical Defense Architecture
Integration of digital systems with physical protection:
Real-Time Monitoring Integration
Active systems providing exposure intelligence:
- Chemical sensor integration: Detection systems providing real-time threat data
- Exposure threshold monitoring: Continuous tracking of compound concentrations
- Barrier integrity verification: Systems confirming protection performance
- Physiological parameter tracking: Monitoring of user vital signs during chemical exposure
- Remaining duration calculation: Predictive analytics for protection timeframes
Next-Generation Response Systems
Advanced technologies for dynamic threat adaptation:
- Compound-specific alarm integration: Targeted alerts based on particular chemical threats
- Automatic defense escalation: Systems increasing protection based on detection
- Remote monitoring connectivity: Team-based awareness of individual exposure status
- Evacuation path optimization: Guidance systems identifying safest exit routes
- Post-exposure documentation: Automated recording of chemical interaction events
Testing and Certification Frameworks
Advanced validation of chemical defense performance:
Saudi-Specific Test Protocols
Validation frameworks reflecting Kingdom's industrial realities:
- Process-authentic chemical testing: Validation using actual industrial compounds
- Multi-vector exposure simulation: Testing against varied contact scenarios
- Desert climate integration: Performance verification under Saudi environmental conditions
- Extended duration validation: Testing against operational timeframe requirements
- Combined stressor protocols: Performance assessment under multiple simultaneous challenges
Comprehensive Certification Standards
Multi-dimensional performance validation frameworks:
- Saudi Aramco specification compliance: Alignment with national energy company requirements
- SASO chemical protection standards: Adherence to Saudi regulatory frameworks
- International standard harmonization: Compliance with global protection benchmarks
- Facility-specific qualification protocols: Validation against site-determined requirements
- Operational performance verification: Real-world validation beyond laboratory testing
Implementation Strategy Framework
Structured approach to chemical defense system deployment:
Threat-Specific Protection Selection
Methodology for identifying optimal defense architecture:
- Chemical hazard profiling: Comprehensive analysis of compound-specific threats
- Exposure pathway assessment: Identification of potential chemical interaction routes
- Operational parameter mapping: Documentation of task requirements affecting protection
- Environmental condition evaluation: Analysis of factors influencing chemical defense
- Protection level classification: Strategic categorization of required safeguarding intensity
Progressive Implementation Architecture
Systematic deployment of advanced protection systems:
- Risk-prioritized deployment: Strategic implementation sequence based on hazard severity
- User adaptation programming: Structured training on advanced system utilization
- Operational integration planning: Alignment of protection with work processes
- Performance verification protocols: Continuous assessment of protection effectiveness
- System optimization framework: Ongoing refinement based on field experience
Future Chemical Defense Horizons
Emerging technologies reshaping protection paradigms:
- Intelligent reactive barriers: Systems autonomously adapting to specific chemical threats
- Catalytic neutralization technology: Protection actively decomposing hazardous compounds
- Biomimetic defense systems: Protection inspired by biological chemical resistance mechanisms
- Predictive exposure management: AI-enhanced systems anticipating chemical threats
- Chemical-specific countermeasures: Targeted defense activation against particular compounds
- User-customized protection profiles: Systems calibrated to individual physiological characteristics
- Micro-robotic defense enhancement: Nanoscale systems actively maintaining protection integrity
Conclusion: Strategic Chemical Defense Imperative
For Saudi organizations operating in chemical-intensive industrial environments, the implementation of advanced chemical defense architecture represents a critical operational investment extending far beyond basic regulatory compliance. The strategic selection of next-generation protection systems delivers measurable advantages in worker safety, operational capability, and process efficiency that directly impact organizational performance.
Leading Saudi enterprises recognize that chemical protection is no longer a commoditized procurement decision but rather a sophisticated engineering challenge requiring systems-level thinking. By implementing quantum-engineered defense systems specifically calibrated for the Kingdom's unique industrial chemical profiles, forward-thinking organizations are establishing new benchmarks in both worker protection and operational excellence in an increasingly competitive global marketplace.
About the Author
Dr. Mohammed Al-Zahrani serves as Director of Chemical Protection Systems at the Saudi Industrial Safety Institute. With a Ph.D. in Chemical Engineering from King Fahd University of Petroleum and Minerals and specialized certification in Advanced Barrier Technology, he focuses on developing next-generation defense systems for extreme chemical environments. Dr. Al-Zahrani has led multiple research initiatives on molecular protection architecture and regularly advises Saudi Aramco, SABIC, and the Royal Commission for Jubail and Yanbu on chemical safety implementation strategies.
Share Article
Related Articles
Chemical Defense Assessment
Commission a comprehensive evaluation of your organization's chemical protection strategy and discover advanced optimization opportunities for enhanced safety performance and operational efficiency.
Request Assessment