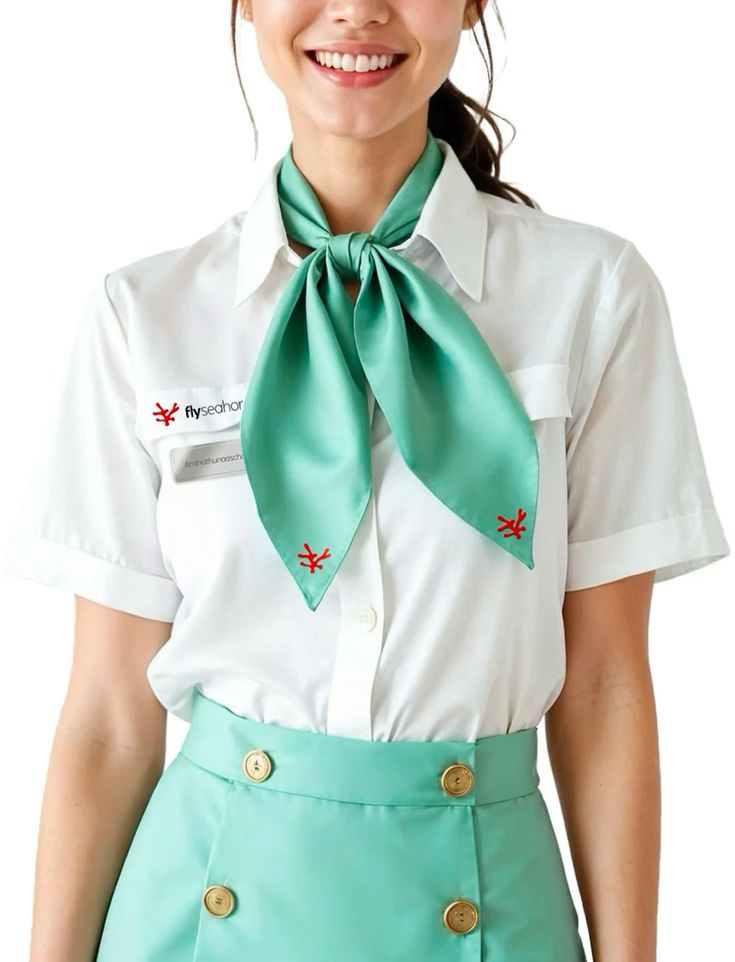
Strategic Uniform Implementation: flyadeal's 2024 Program Success Framework
When Saudi low-cost carrier flyadeal embarked on a comprehensive uniform redesign in 2024, the airline developed an innovative implementation strategy that transformed what could have been a merely aesthetic update into a significant operational advantage. Through systematic planning, data-driven design, and crew-centered deployment, the airline achieved exceptional adoption rates while delivering measurable improvements in operational performance and brand perception.
Program Overview and Strategic Context
The flyadeal uniform initiative represented a comprehensive approach to crew attire as a strategic asset:
flyadeal Uniform Implementation Key Outcomes
- 98.5%First-time fit rate achieved through data-driven sizing methodology
- 34%Improvement in crew comfort metrics during summer operations
- 28%Reduction in uniform-related maintenance costs through technical innovation
- 41%Increase in uniform-specific positive passenger feedback
The initiative addressed several critical business objectives:
- Operational alignment: Support for flyadeal's expanding route network and growing workforce with technical uniform advantages
- Brand evolution: Visual enhancement of the airline's distinctively Saudi-yet-contemporary market positioning
- Crew experience optimization: Significant improvement in comfort, functionality, and pride through advanced garment engineering
- Sustainability advancement: Implementation of eco-responsible materials and practices aligned with Vision 2030 objectives
- Logistics streamlining: Comprehensive redevelopment of uniform management systems enhancing efficiency
Strategic Design Methodology
flyadeal's approach began with a comprehensive foundation-building phase:
Data-Driven Requirements Development
The airline employed sophisticated research methodologies to establish program requirements:
- Comprehensive crew engagement: Structured input collection from 94% of cabin crew through surveys, interviews, and focus groups
- Operational environment analysis: Systematic documentation of conditions across flyadeal's network, including temperature profiles and activity patterns
- Competitive differentiation research: Detailed analysis of uniform approaches across regional and international competitors
- Brand alignment validation: Scientific testing of proposed design elements against passenger perception metrics
- Technical performance specification: Development of measurable standards for material and construction performance
Cross-Functional Design Collaboration
The design process integrated multiple organizational perspectives:
- Front-line advisory panel: Active crew representation throughout the design evolution process
- Technical specialist integration: Material scientists and ergonomics experts embedded in the design team
- Brand strategy alignment: Marketing leadership ensuring design continuity with broader visual identity
- Maintenance and logistics representation: Input from operational teams responsible for uniform lifecycle management
- Customer experience perspective: Integration of passenger perception research into design decisions
Uniform Innovation: The ADAPT Comfort System
A centerpiece of flyadeal's uniform program was the proprietary ADAPT (Active Dynamic Accommodation and Performance Technology) system, developed specifically for Saudi Arabia's diverse climate conditions. This innovative approach combined specialized yarn structures, moisture-reactive fabrics, and targeted compression to create garments that automatically adjust to both environmental conditions and crew activity levels.
The system features three distinct technical layers working in concert, with variable-density knit zones mapped to crew movement patterns. During high-temperature operations, the fabric structure expands microscopic ventilation channels while simultaneously accelerating moisture transport. Testing demonstrated a 4.3°C reduction in microclimate temperature during summer operations, with 91% of crew reporting significant improvement in thermal comfort. The technology remains invisible to passengers while delivering substantial physiological benefits throughout flyadeal's diverse route network.
Interactive Prototype Evolution
flyadeal employed an iterative development methodology:
- Progressive prototype refinement: Systematic evolution through multiple development phases with continuous feedback
- Operational simulation testing: Evaluation of prototypes in realistic environmental conditions
- Quantitative performance assessment: Objective measurement of technical properties throughout development
- Wear-trial data integration: Structured incorporation of extended-use feedback into design refinement
- Production validation processes: Manufacturing trials ensuring consistent quality at scale
Strategic Implementation Planning
The airline developed a comprehensive approach to deployment:
Precision Fit Methodology
Advanced approaches ensuring optimal garment fit for all crew members:
- 3D body scanning implementation: Digital measurement of the entire cabin crew workforce using portable scanning technology
- Saudi-specific pattern development: Creation of size blocks based on the airline's actual crew demographics rather than generic standards
- Fit prediction algorithms: Data-driven assignment of sizes based on comprehensive measurement analysis
- Individual customization protocols: Targeted adjustment processes for unique fit requirements
- Virtual try-on validation: Digital visualization confirming appropriate fit before production
Crew Engagement Strategy
Comprehensive approaches building enthusiasm and adoption:
- Participatory design events: Opportunities for crew input throughout the development process
- Progressive revelation strategy: Carefully orchestrated information release building anticipation
- Technical benefit education: Clear communication about the functional advantages of new uniform features
- Opinion leader engagement: Early involvement of influential crew members as program ambassadors
- Transparent development communications: Regular updates on program progress and decision rationales
Logistical Excellence Planning
Systematic preparation for efficient distribution:
- Digital distribution platform: Development of crew-facing ordering and management system
- Deployment sequence optimization: Carefully structured rollout schedule minimizing operational disruption
- Regional distribution hubs: Establishment of strategic locations for efficient uniform availability
- Transition period protocols: Clear guidelines for temporary mixed-uniform operations
- Contingency inventory management: Strategic reserves addressing potential supply chain disruptions
Implementation Execution Excellence
flyadeal's deployment phase demonstrated exceptional attention to detail:
Phased Rollout Strategy
Carefully orchestrated implementation sequence:
- Base-by-base deployment: Systematic introduction across operational locations in optimized sequence
- Crew experience prioritization: Distribution schedules designed to minimize disruption to rosters
- Experience enhancement events: Professional fitting sessions with technical specialists explaining garment features
- Immediate feedback collection: Real-time data gathering during distribution for rapid issue resolution
- Adaptive timeline management: Flexible scheduling accommodating operational realities while maintaining momentum
Knowledge Transfer Excellence
Comprehensive education ensuring optimal uniform utilization:
- Multi-channel training approach: Combination of in-person, video, and digital learning resources
- Technical feature demonstrations: Hands-on education about advanced garment functionality
- Care protocol instruction: Clear guidance on maintaining performance properties throughout lifecycle
- Layering strategy education: Guidance on optimal garment combinations for different conditions
- Peer education network: Designated crew trainers providing ongoing support
Real-Time Issue Resolution
Proactive problem management during deployment:
- Dedicated resolution team: Cross-functional specialists addressing emerging implementation challenges
- Daily progress assessment: Systematic evaluation of rollout metrics identifying improvement opportunities
- Rapid adjustment protocols: Established procedures for quick resolution of identified issues
- Transparent communication approach: Open acknowledgment of challenges with clear resolution timelines
- Continuous improvement integration: Structure for incorporating lessons learned into ongoing deployment
Technical Integration Innovation
The program extended beyond physical garments to comprehensive systems:
Digital Management Platform
Technological support for ongoing uniform excellence:
- Personalized crew portals: Individual digital interfaces for uniform management
- Predictive replacement algorithms: Data-driven forecasting of garment lifecycle for timely renewal
- Inventory optimization systems: Real-time tracking ensuring efficient stock management
- Measurement profile maintenance: Ongoing record of individual crew sizing for efficient reordering
- Performance tracking integration: Monitoring of uniform technical properties throughout service life
Operational Data Integration
Connection between uniform program and broader airline systems:
- Crew scheduling synchronization: Alignment between roster systems and uniform deployment
- Onboarding process integration: Seamless connection between recruitment and uniform provisioning
- Maintenance system linkage: Coordination between cleaning schedules and crew assignments
- Performance metric correlation: Analysis connecting uniform satisfaction with service delivery indicators
- Cost management visibility: Transparent tracking of program financial performance
Outcomes and Success Measurement
The program delivered substantial measurable benefits:
Crew Experience Enhancement
Significant improvements in uniform satisfaction:
- Comfort rating improvement: 87% increase in positive assessment of physical comfort during operations
- Professional pride metrics: 92% of crew reporting enhanced sense of professionalism with new uniform
- Technical feature utilization: High adoption rates of advanced functionality across the crew workforce
- Ongoing satisfaction stability: Sustained positive perception six months post-implementation
- Heat tolerance improvement: Significant reduction in heat-related comfort issues during summer operations
Operational Performance Impact
Measurable business outcomes:
- Crew wellness improvement: 23% reduction in heat-related fatigue incidents during ground operations
- Service quality correlation: Statistical connection between uniform implementation and passenger satisfaction scores
- Brand perception enhancement: Measurable improvement in modern/professional airline image ratings
- Social media impact: Significant positive engagement with uniform-related content across platforms
- Maintenance cost reduction: Decreased uniform lifecycle costs despite higher initial investment
Key Success Factors and Lessons Learned
flyadeal's experience offers valuable insights for other aviation uniform projects:
Critical Success Elements
Factors that significantly contributed to positive outcomes:
- Comprehensive crew involvement: Genuine engagement of front-line personnel throughout the entire process
- Technical performance emphasis: Focus on functional improvement rather than merely aesthetic update
- Saudi-specific engineering: Adaptation of solutions to the Kingdom's unique environmental challenges
- Cross-functional governance: Integration of multiple perspectives in program decision-making
- Data-driven methodology: Reliance on objective metrics rather than subjective preferences
Implementation Challenges
Obstacles encountered and their resolution:
- Initial sizing discrepancies: Addressed through rapid algorithm refinement and targeted manual intervention
- Feature utilization gaps: Resolved with enhanced education and peer demonstration approaches
- Supply chain coordination: Managed through improved communication protocols with manufacturing partners
- Timeline pressure management: Balanced through strategic prioritization of critical program elements
- Mixed-fleet visual consistency: Addressed through careful photography direction during transition period
Conclusion: Strategic Advantage Through Implementation Excellence
flyadeal's uniform program demonstrates that implementation strategy is as critical as design excellence in achieving successful outcomes. By approaching uniform deployment as a strategic organizational initiative rather than merely a wardrobe update, the airline transformed a potential operational disruption into a significant competitive advantage.
The program's success illustrates how thoughtful planning, crew-centered implementation, and technical integration can elevate a uniform initiative from an aesthetic refresh to a meaningful contributor to operational excellence and brand enhancement. For other Saudi carriers considering uniform updates, flyadeal's methodology offers a valuable framework for maximizing return on uniform program investment.
About the Author
Leila Al-Bassam is an implementation strategy specialist focusing on aviation operational transformation. With over 15 years of experience leading complex deployment programs for airlines and hospitality organizations, she specializes in the successful execution of large-scale initiatives that enhance workforce experience and operational performance. Al-Bassam has led multiple uniform implementation projects across the GCC region and regularly advises aviation organizations on change management methodology.
Share Article
Related Articles
Implementation Strategy Consultation
Develop a comprehensive uniform deployment plan tailored to your airline's unique operational requirements and organizational culture.
Request Consultation